Прошлой осенью мы взяли на длительный тест незаменимую в хозяйстве любого любителя техники для активного отдыха штуку — мотоприцеп «Тайга-2» производства компании «Курганские прицепы». Снегоходы, квадрики, кроссовые мотики, гидроциклы — все эти замечательные аппараты не предназначены для самостоятельного перемещения по дорогам общего пользования, и поэтому без прицепа просто никуда. Прицеп, сам по себе, штука довольно обыденная, но уж коли взялись изучать вопрос плотно, то нужно вникать во все. Именно поэтому мы отправились в западно-сибирский город Курган на завод, где производятся эти транспортировочные средства.
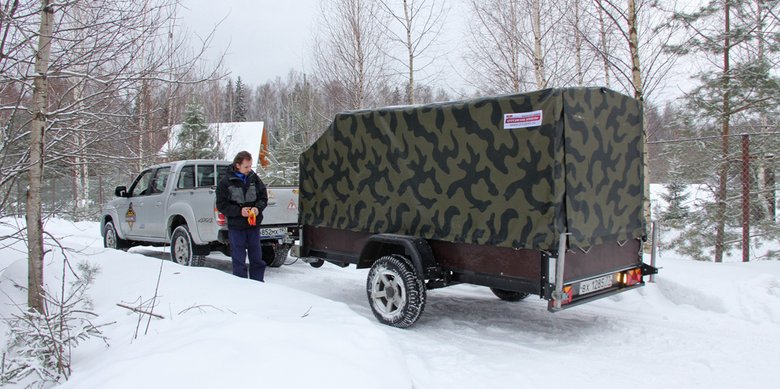
Город Курган — областной центр на юге западной Сибири. Довольно крупный индустриальный и сельскохозяйственный город. Но, кто бы мог подумать, что здесь, вдали от оживленных трасс, родилось производство прицепов? Здесь расположен «хитрый» военный завод, основной продукцией которого является военная техника. Но в скудные на госзаказы 90-е, как и на многих оборонных предприятиях, тут начали искать способы зарабатывать на конверсионной продукции. Так родилась прицепная тема.
Со временем производство отделилось в самостоятельную компанию, заметно расширился модельный ряд и объемы. Тем не менее, уровень качества и запас прочности, которые вкладывают в свою продукцию заводчане, до сих пор попахивают тяжелой бронетехникой, которая у нас, в России, по-прежнему одна из лучших в мире.
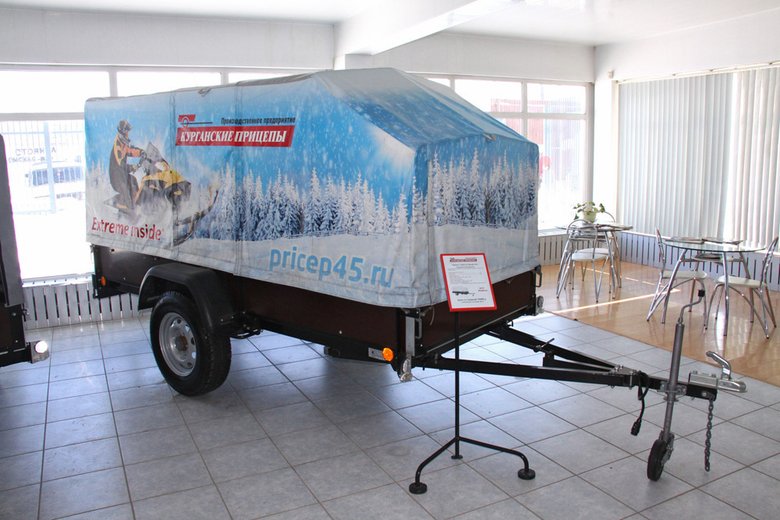
Экскурсию по заводу проводил главный конструктор предприятия — Владимир Астафьев. Разговор мы начали еще на улице, на подходе к первому цеху. Владимир Николаевич начал разговор с общей картины: на российском рынке сейчас есть три наиболее крупных производителя прицепов, в частности, производящих прицепы для мототехники. Конкуренция довольно сильная, и единственный выход оставаться на плаву — делать продукт более качественным, удобным в использовании, надежным и, естественно, недорогим. Именно в этих направлениях и идет работа. Основной инструмент, направленный на выполнение всех этих требований, — минимальная зависимость от сторонних производителей.
Первый — цех подготовки производства. Все модели, от самого маленького снегоходно-квадроциклетного прицепа «Трофи» до флагмана «Тайга−2», начинают свою жизнь тут. Уже в этом цеху понимаешь, что подразумевают заводчане, когда говорят о максимальной локализации производства. Ведь только на первый взгляд кажется что прицеп — это четыре куска арматуры, два колеса и дышло.

Здесь, в цехе подготовки производства, рождаются почти все основные элементы будущего прицепа. Режется профиль для рам и дышел, пруток для стоек и арматуры, из листа штампуются борта и мелкие комплектующие. Более сложные элементы конструкции вырезают из листовой стали на нескольких плазморезах с цифровым управлением. Здесь же, рядом сваривают будущие рамы прицепов.
Токарное и фрезерное оборудование тоже не из прошлого века. Все станки работают под контролем ЧПУ, так что качество деталей всегда одинаковое и не зависит от дня недели, квалификации мастера и его физического состояния. Здесь же несколько вулканизационных машин, на которых из сырой резины разных сортов изготавливают втулки и сайлент-блоки для подвески. Даже такие, вроде бы, мелочи, и те производят на заводе сами, а не закупают на стороне.
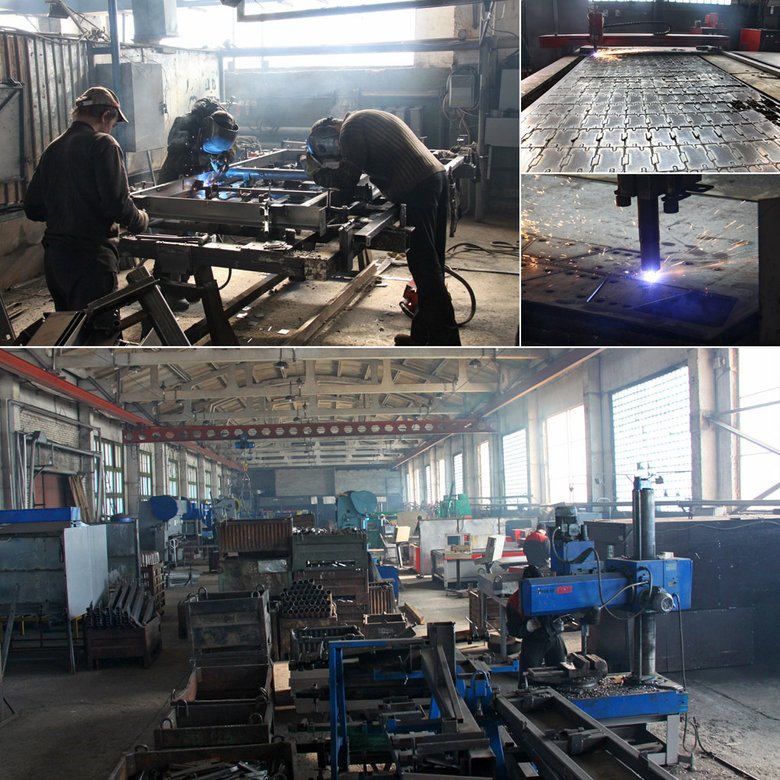
Кстати, о подвеске — после нескольких экспериментов в фирме пришли к выводу, что невозможно адаптировать под прицеп какие-то разработанные для других типов ТС подвески. Для каждого типа прицепа подвеска разрабатывается индивидуально. На самых маленьких моделях — это пружинно-гидравлическая схема, на более грузоподъемных — рессорно-гидравлическая с прогрессивной характеристикой (при малых нагрузках работает не вся рессора, а только несколько листов, а по мере увеличения нагрузки, они проседают, и в дело включаются дополнительные листы, увеличивая общую жесткость системы). Никаких рессор от «Газели» или других попыток «скроить». Все рассчитывается индивидуально.
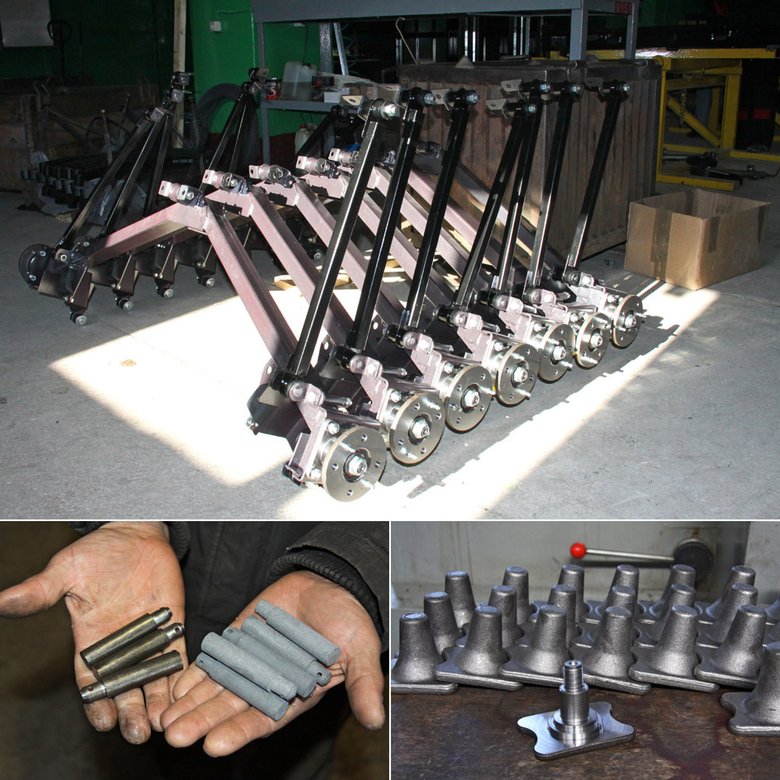
Сами элементы подвески по большей части изготавливают здесь же. Специально для «КП» на металлургическом комбинате штампют заготовки и уже здесь на собственном оборудовании из них точат ступицы. Замечу, что даже тут не обошлось без инженерии. Большинство прицепов могут комплектоваться колесами разного диаметра. От 13 дюймов, под обычные «Жигули», до 16 — под прицепы для внедорожников и малотоннажных грузовиков. Это делается для того, чтобы колеса в составе автопоезда были одинакового, или, хотя бы, близкого размера. Все ради стабильности на ходу и управляемости автопоезда. Так вот, даже ступицы под маленькие и большие колеса отличаются по размеру и конструкции. Никакого лишнего веса и тем более недостатка прочности. Любая конструкция получается оптимально сбалансированной по запасу прочности.
Далее готовые металлические части отправляются в цех окраски. Как и в случае с автомобилями, задача краски не столько художественная, сколько практическая — защитить металлические части от коррозии. Сначала детали проходят пескоструйную обработку — так удаляют остатки коррозии, грязь и прочие ненужные включения с поверхности металла. После этого детали поступают на окраску. Здесь применяют только порошковый метод окраски. Порошок наносят на металл электростатическим напылением, а потом запекают в специальных печах. Порошок спекается в монолитный слой и крепко соединяется с металлом. Такой тип покрытия на сегодняшний день считается наиболее коррозионно-стойким.
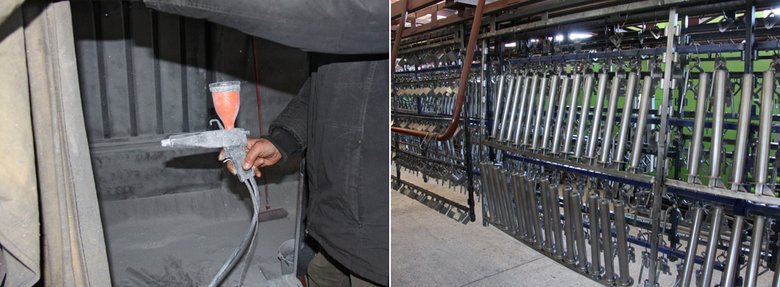
Не забывают здесь и об эстетической составляющей. Если в базовом, наиболее бюджетном варианте, борта прицепов оцинкованные, то за небольшую доплату можно выбрать из более чем десятка цветов. Правда, в основном, это касается прицепов хозяйственного назначения. «Телеги» большего калибра оборудуют бортами и полами из ламинированной водостойкой фанеры, которая не боится воды, морозов и едких реагентов, которыми поливают наши дороги.
Отдельный, совсем небольшой цех занимается изготовлением электропроводки. Вроде бы, что там проводов-то, в прицепе, однако и здесь требуется качество. Ночью остаться без света на прицепе — не самое веселое дело.
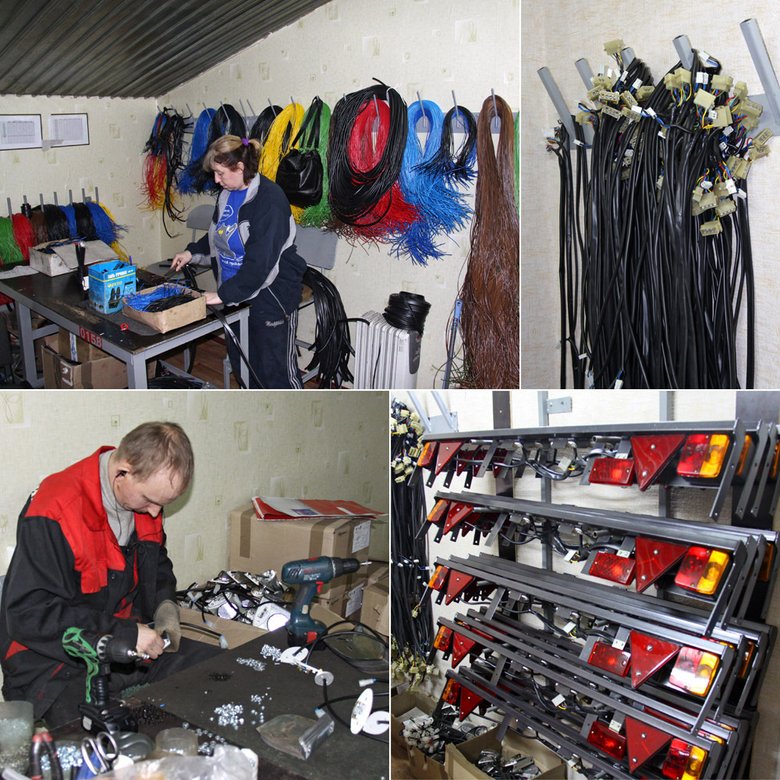
Женское «царство» фирмы — обычно это бухгалтерия. Однако на «Курганских прицепах» это швейный цех. Здесь полтора десятка работниц кроят и шьют тенты для всей линейки фирмы. Плотный ПВХ обычно серого, синего или камуфляжного цвета, однако, по особой договоренности, можно заказать тент иного цвета и даже с нанесенным индивидуальным рисунком.
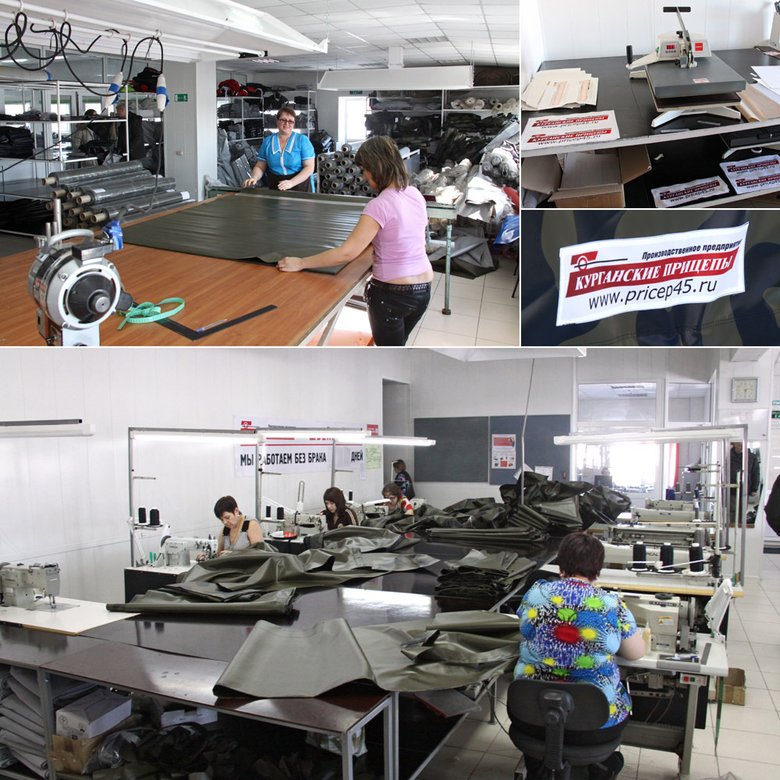
Теперь, когда основные элементы конструкции изготовлены, они поступают в сборочный цех. Именно сборка — наиболее яркий показатель качества изготавливаемой продукции. Многие, кто хоть раз был на машиностроительном предприятии, знают, что неотъемлемым инструментом любого сборочного процесса в советской стране была кувалда, которая хранилась в секретной тумбочке. В случае возникновения несоосности отверстий или диаметров отверстия и болта, да мало ли чего к чему не подходило как положено (что случалось повсеместно и регулярно), один сборщик отправлялся отвлекать тетку-инспектора ОТК, а другой тем временем извлекал заветный инструмент и дорабатывал необходимую нестыковку простым и понятным способом. Правда, после этого все разваливалось, но это происходило уже у покупателя и мало кого волновало.
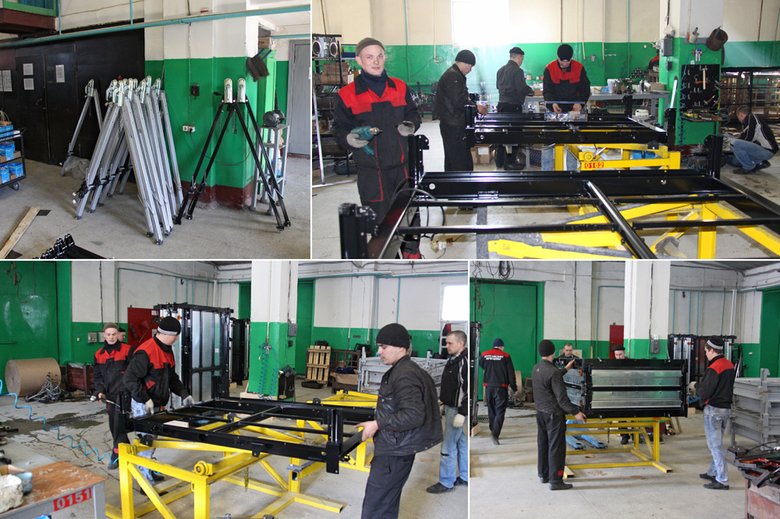
Так вот, здесь сборка происходит без кувалды, напильника и каких-либо других вспомогательных недокументированных средств. На сборку даже самого большого прицепа у бригады из четырех человек уходит не больше 15 минут! Стоит заметить, правда, что прицепы здесь собирают не полностью. Для удобства транспортировки собирают только «корыто» прицепа, укладывают и подключают проводку, устанавливают борта. Подвеску, дышла и каркас тента, если таковой имеется у модели, а также колеса (все в двух экземплярах), укладывают внутрь и накрывают таким же «полуфабрикатом». Получается весьма компактная конструкция, этакий параллелепипед, почти не имеющий выступающих частей.
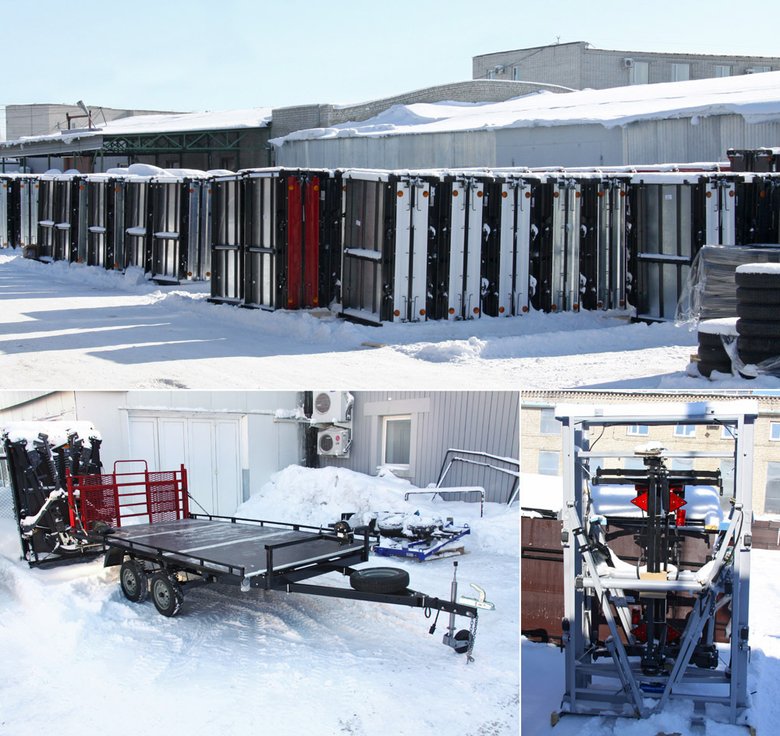
В таком виде прицепы и отправляются на склад готовой продукции и разъезжаются по всей стране — к дилерам. Окончательную сборку проводят уже на месте. Два опытных механика тратят на окончательную сборку одного прицепа от двадцати минут до полутора часов, в зависимости от модели.
В общем-то, довольно заурядный технологический процесс. Но приятно удивили именно те вещи, на которые с первого взгляда не обращаешь внимания. Очень серьезное внимание, уделяемое, вроде бы, мелочам: и возможность выбора диаметра колес, и регулировки клиренса на некоторых моделях, и наличие огромного количества комплектаций прицепов и аксессуаров — все сделано для того, чтобы эксплуатация прицепа была максимально комфортной.
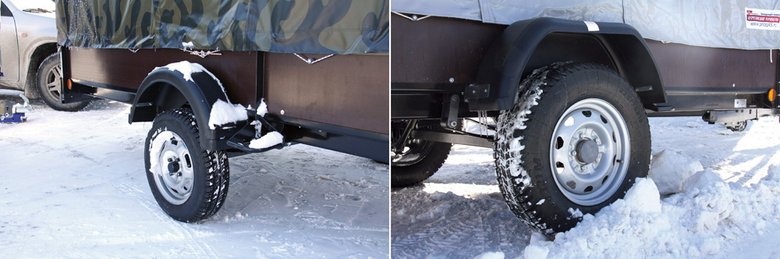
Еще один факт, который меня, как человека, непосредственно связанного с разного рода мототехникой, очень порадовал — это количество моделей, разработанных специально для таких, как я. Наша , пожалуй, топовая модель линейки. Здесь есть все, что только можно придумать: самосвальная система с фиксацией в обоих положениях, релинг для установки мотоцикла с упором для колеса, лебедка для погрузки и разгрузки техники, упоры, не позволяющие прицепу опрокинуться, если он не «пристегнут» к автомобилю, и даже такая мелочь, как специальная ступенька у бокового полога, чтобы удобнее было забираться внутрь. Вроде бы, такие мелочи, но как облегчают жизнь!
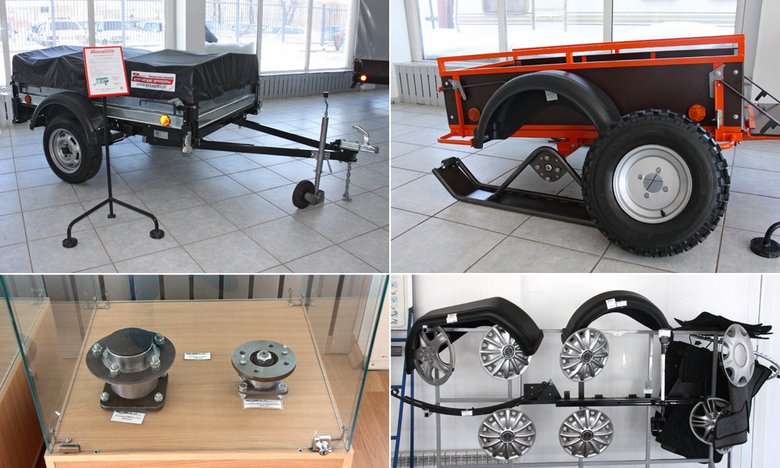
Так вот, о разнообразии — в линейке фирмы есть прицеп для квадриков. Он похож на нашу «Тайгу», но покороче. Есть модель «водник», для перевозки лодок и гидроциклов, есть совсем уж огромный прицеп-платформа «Тандем», на который запросто умещаются два квадрика поперек или два снегохода «валетом», или один SSV. Самый младший в семействе — прицеп «трофи». Он разработан специально для того, чтобы таскать его за квадроциклом. Даже колеса у него — от квадрика, зубастые. А зимой колеса легко меняются на полозья, и прицеп превращается в снегоходный. Можно смело грузить до 400 килограммов. Насколько я знаю, на данный момент никто в России такого еще не «изобрел»! Такое внимание к квадроциклистам, снегоходчикам и прочим любителям внедорожной техники для меня было приятным и удивительным. Вроде бы, Курган — далеко не самый «моторизованный» край, ан нет.
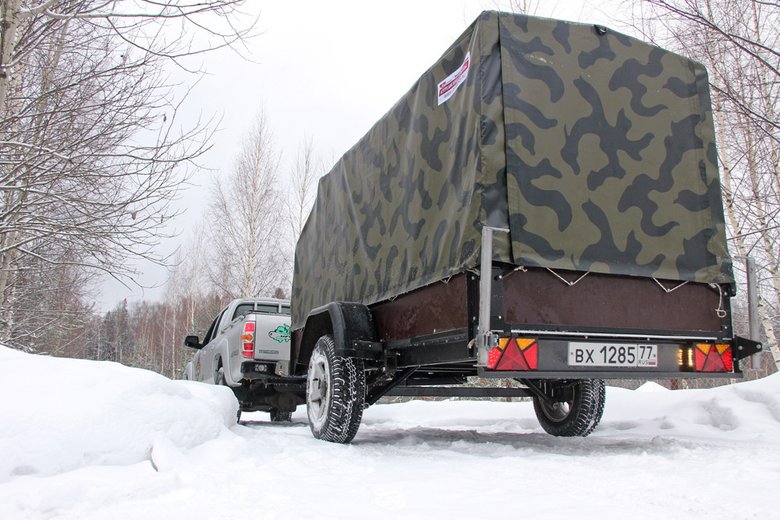
В общем, экскурсия по заводу убедила меня в том, что наш прицеп прослужит нам не один год. Можно не ждать от него сюрпризов вроде выпавших по дороге забитых молотком болтов и лопнувших рессор. А значит, можно смело оправляться в дорогу.
Благодарим компанию «ТД Курганские прицепы» за помощь в подготовке материала.