Барабанная дробь. В престижном конкурсе «Завод года» победу одержала... сборочная площадка компании MAN, где выпускают тяжёлые грузовики серий TGS и TGX. А находится производство неподалёку от Кракова, поэтому правильный ответ — Польша. Между прочим, это уже вторая победа мановского конвейера: впервые престижную награду, которую выдают эксперты профильного журнала Produktion («Производство»), предприятие получило 3 года назад.
Так чем польский заводик дважды удивил специалистов? Уж точно не размерами. Производственная площадка имеет крохотные по автомобильным меркам масштабы — 225 000 квадратных метров. О глубине локализации тоже говорить не приходится. Это чисто сборочное производство: ежедневно сюда приезжает по 80 грузовиков, которые привозят абсолютно все необходимые компоненты — двигатели, кабины, мосты и даже рамы.
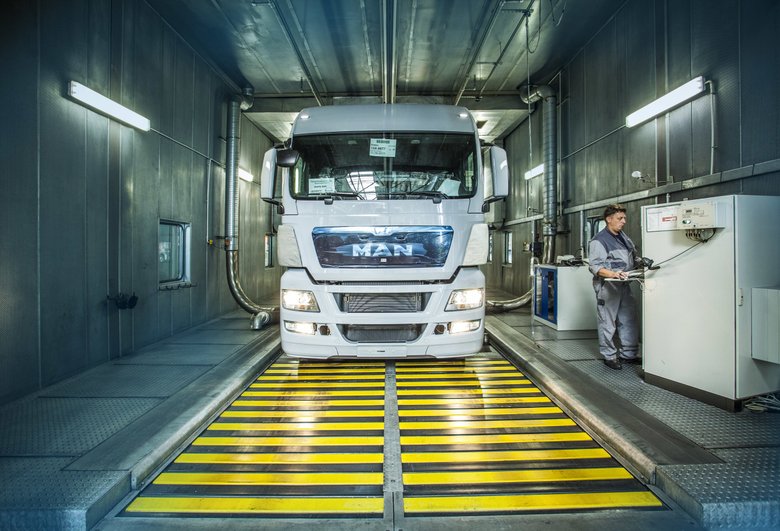
С другой стороны, здесь делают двух-, трёх- и четырёхосные грузовики различных конфигураций, которые затем отправляются по всему миру — в страны Европы, Африки и Азии. В 2018 году завод силами 750 сотрудников выпустил около 20 000 автомобилей. Много это или мало? Огромнейший КАМАЗ может ежегодно выпускать более чем втрое больше машин — 71 тысячу. При численности штата 33 500 человек (правда, КАМАЗ делает массу комплектующих, но сейчас не об этом).
Собственно, команда — главная гордость завода. 98% работников — граждане Польши. При отнюдь не баснословной зарплате (около 1 000 евро) сотрудники очень дорожат своими местами, потому что имеют массу стимулов. Редко болеешь? Получи прибавку. Оформил рацпредложение? Держи премию. Плюс компенсация расходов на фитнес-клуб. А ещё свой собственный фитнес прямо на территории завода. Плюс столовая, медкабинет и много других «плюшек».
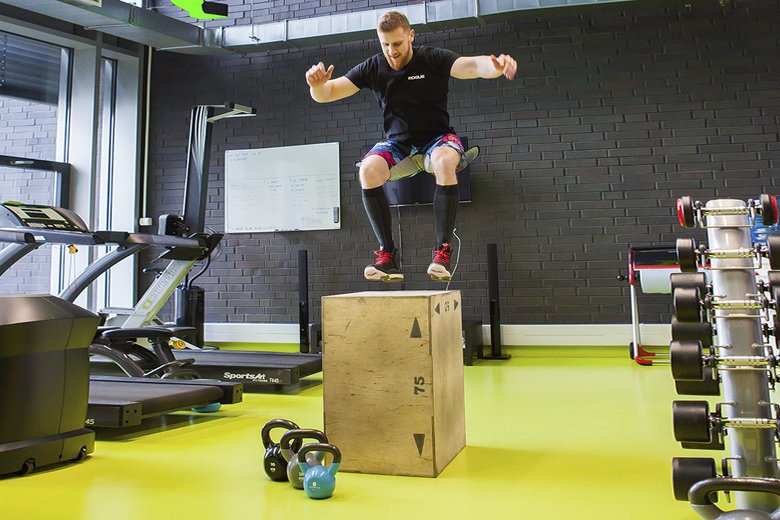
Большая часть штата — креативная молодёжь (им даже разрешают ставить на сборочных постах магнитофоны, чтобы негромко слушать музыку). Настолько креативная, что небольшой польский завод регулярно занимает первое место среди всех производств огромной группы Volkswagen по числу внесённых рацпредложений! Кстати, сотрудникам разрешено носить шорты, а для передвижения использовать самокаты — такого мы точно не видели больше нигде.
По качеству грузовики польской и немецкой сборки абсолютно одинаковы, а заказы между европейскими заводами MAN распределяются по принципу «где есть свободные места». Что касается контроля качества, то на предприятии под Краковом действует многоуровневая система. Последняя включает стопроцентный контроль приходящих компонентов, а также последовательную проверку собираемой машины на трёх постах конвейера.
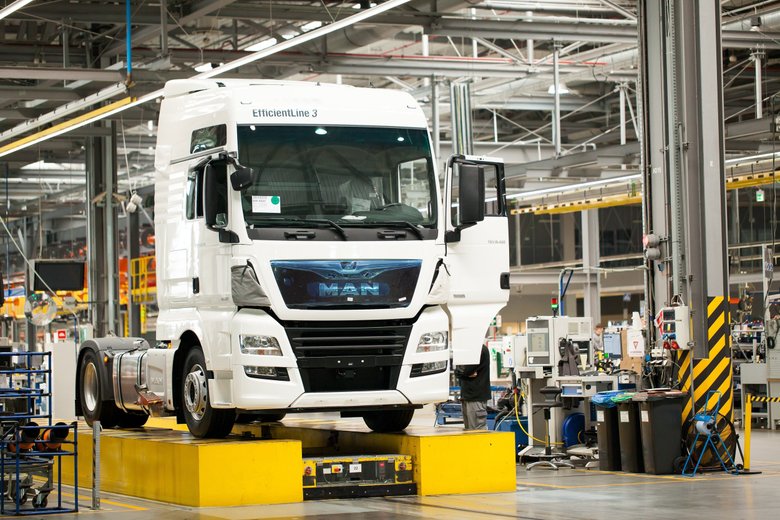
Финальная проверка включает тестирование тормозов, калибровку тахографа и многое другое. При этом грузовик разгоняют на стенде до 110 км/ч, а при желании заказчика — до 130 км/ч. Ежедневно одну случайно выбранную машину вдобавок отправляют на заводской полигон, где она накатывает 100 километров. Перед сдачей грузовика клиенту автомобиль осмотрят ещё раз — на предмет повреждений, которые могли случиться при транспортировке.
Главная сложность — в специфике выпускаемой продукции: каждый собираемый грузовик абсолютно уникален — по конструкции, комплектации и даже... стране, где ему предстоит ездить. Например, тягачу, который заказал российский перевозчик, поставят усиленные рычаги подвески, а для немецкого клиента будет достаточно обычных. Как тут не запутаться? На самом деле, ошибки случаются, но не больше 200 на сотню машин (обычно «косячат» поставщики).
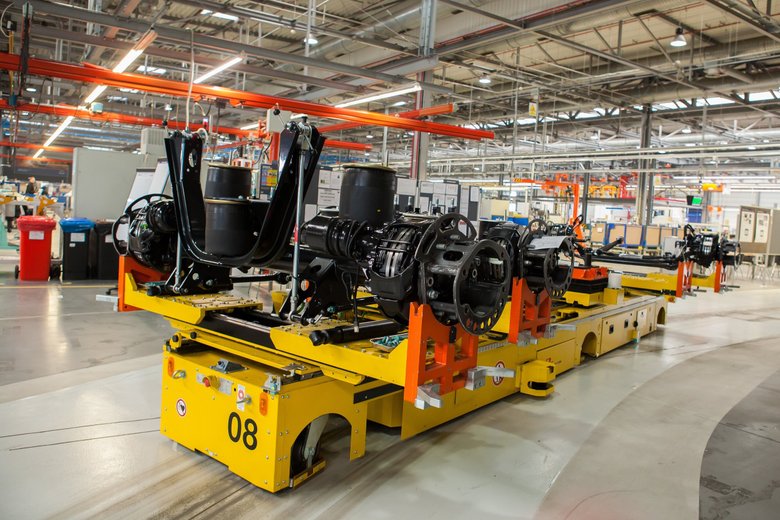
В день сотрудникам конвейера разрешено совершить 10 оплошностей на 100 машин. Однако каждый случай тщательно разбирается, поэтому «нормы по ошибкам» всегда остаются невыбранными. С первой попытки приёмку проходит собранной 70% техники. И этому есть объяснение: «Поставщики не успевают вовремя доставлять нужные компоненты — нам проще собрать автомобиль, а потом подождать, когда пришлют запчасть», — говорят мановцы.
«Когда люди, бывавшие на других заводах, приходят сюда, сразу спрашивают: что, конвейер сегодня стоит?», — улыбается директор Хайко Кайзер. Действительно, сборка грузовиков идёт полным ходом, а в цеху — очень-очень тихо! А всё потому, что каждый будущий грузовик едет на отдельной (и абсолютно бесшумной) электрической тележке. К сборочным постам детали также подвозят беспилотные электрические транспортёры.
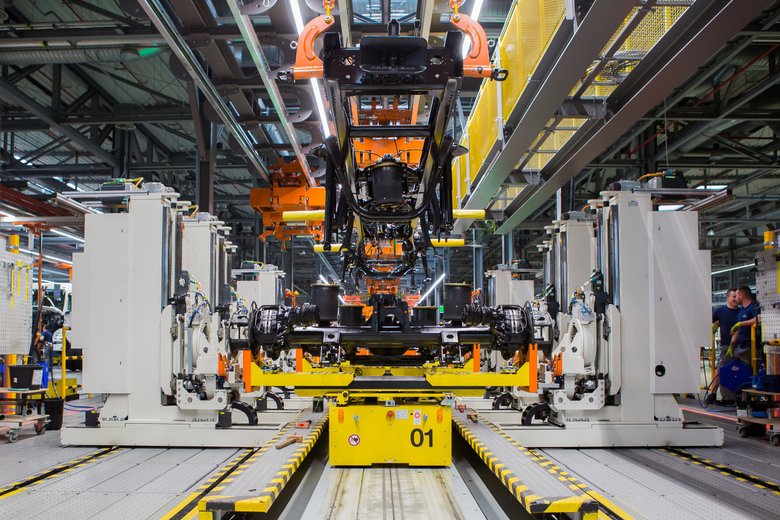
На каждом сборочном посту установлены по 2-3 монитора. Как только въезжает новая тележка, на экранах появляется наглядная информация: к этому грузовику нужно прикрутить это, это и ещё вот это. Совершить ошибку просто невозможно! Кстати, к постам нужные детали подвозятся беспилотниками по принципу «just in time» — в нужное время, в нужное место. Поэтому вдоль сборочной линии нет нагромождения запчастей и ящиков.
Как работает грузовой автозавод: инструкция для чайников
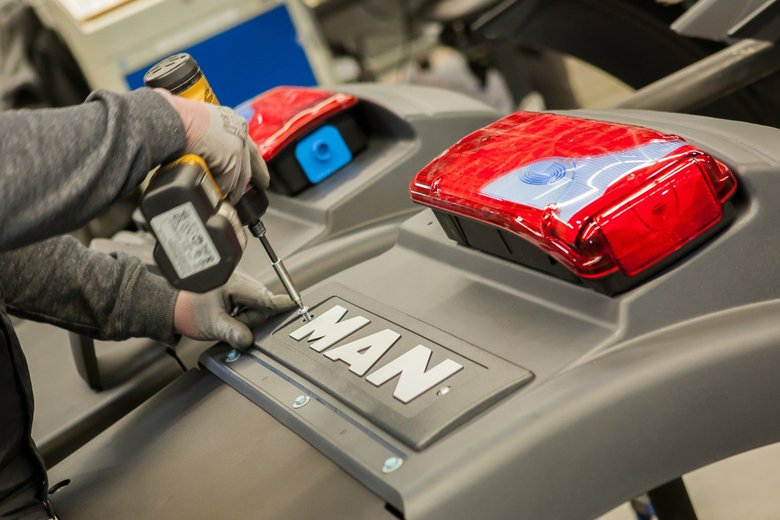
- Сначала берётся рама: её зачищают, грунтуют и дважды красят. После сушки на лонжерон наносится VIN-номер, который может сказать об автомобиле абсолютно всё: количество осей, комплектацию и многое-многое другое.
- Затем начинается сборка — первым делом на стоящую вверх тормашками раму устанавливают подвески. Дальше скелет переворачивают, чтобы самоходная тележка подкатила мосты, а рабочие навесили тормозную систему и установили карданные валы.
- Будущий грузовик, постепенно обрастая деталями (двигателем, кабиной и всем остальным), проходит 900-метровую нитку конвейера за 40 тактов. Подготовка силового агрегата, где стыкуются двигатель и коробка, ведётся на отдельном участке.
- Собранный автомобиль заправляется жидкостями и топливом. После этого начинается работа программиста, чтобы «залить» прошивку, а затем завести автомобиль. Заведённая машина своим ходом отправляется «сдаточной команде».
- В завершении тягачи и шасси гоняют на динамометрическом стенде, а также настраивают им тормозную систему, развал-схождение колёс и многое другое. И уже совсем финальный штрих — проверка качества сертифицированными специалистами.
- Прошедший проверку грузовик отгоняют на внутризаводскую парковку, где ему предстоит дождаться отправки будущему владельцу. Готово! C конвейера готовые машины сходят каждые 9 минут 30 секунд, то есть ежедневный ритм — 95 автомобилей.
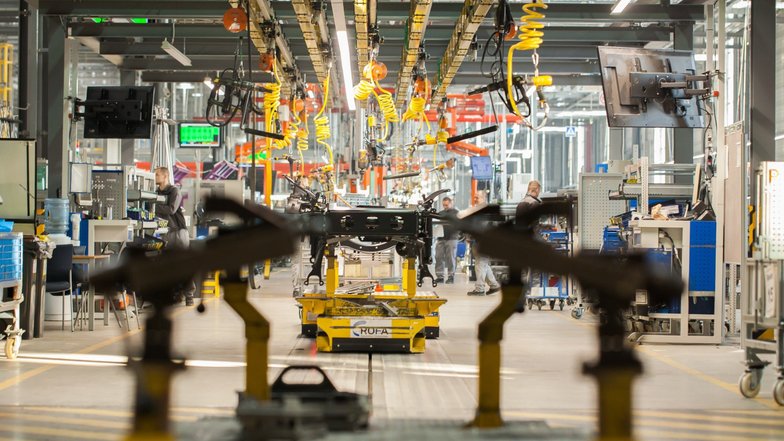
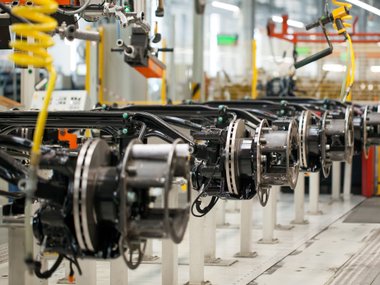
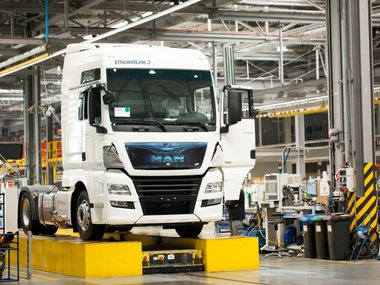
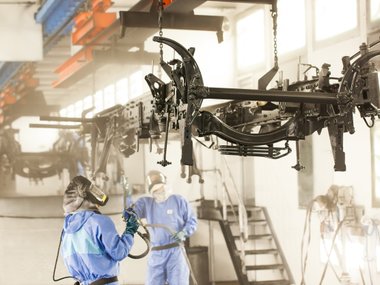
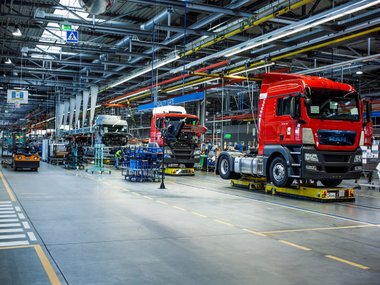