Во время посещения российского завода Hyundai, расположенного в промзоне Каменка, что под Санкт-Петербургом, сразу вспомнилась песенка из фильма «Приключения Электроника»: «Вкалывают роботы, а не человек...». Штамповка, сварка, окраска, сборка — везде роботы! «Уровень автоматизации составляет 80%», — гордо отмечают заводчане. Судя по объемам продаж «Солярисов» (за 10 месяцев реализовано 80 тысяч авто), корейцы не прогадали, вложив в возведение мощностей 500 млн долларов. И если остальные российские заводы полного цикла наращивали объемы производства постепенно, то в Hyundai изначально рассчитывали на выпуск 150 тысяч машин ежегодно. В ближайшем будущем производство «разгонится» до 200 тысяч автомобилей!
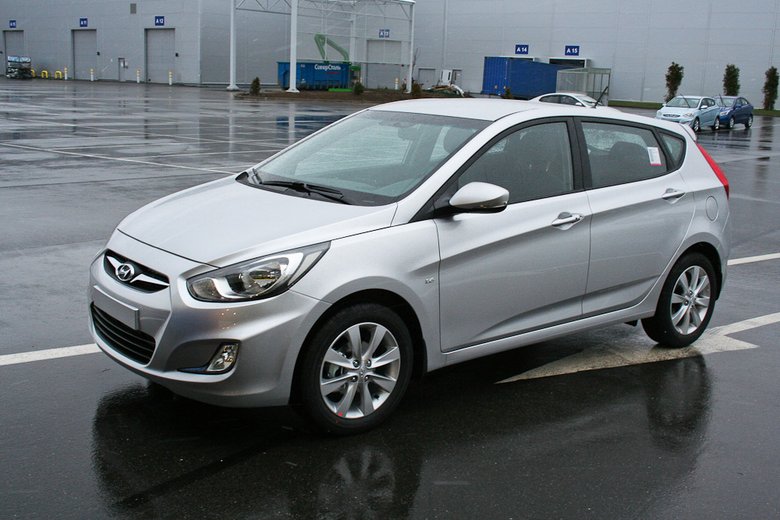
Глядя на стерильную чистоту помещений, красивую униформу и обилие роботов-помощников, понимаешь, почему желающие работать на заводе Hyundai выстраиваются в очередь — условия труда корейцы организовали на отлично. Зарплата хорошая — от 29 тысяч рублей для новичка, только пришедшего на предприятие, плюс объемный соцпакет, включающий медицинскую страховку, питание и доставку до станции метро. Впрочем, и спрашивают строго: за первое опоздание на смену — предупреждение, второе — увольнение. Да и дисциплина больше похожа на армейскую: рабочие стройной колонной отправляются в столовую, строем уходят к конвейеру...
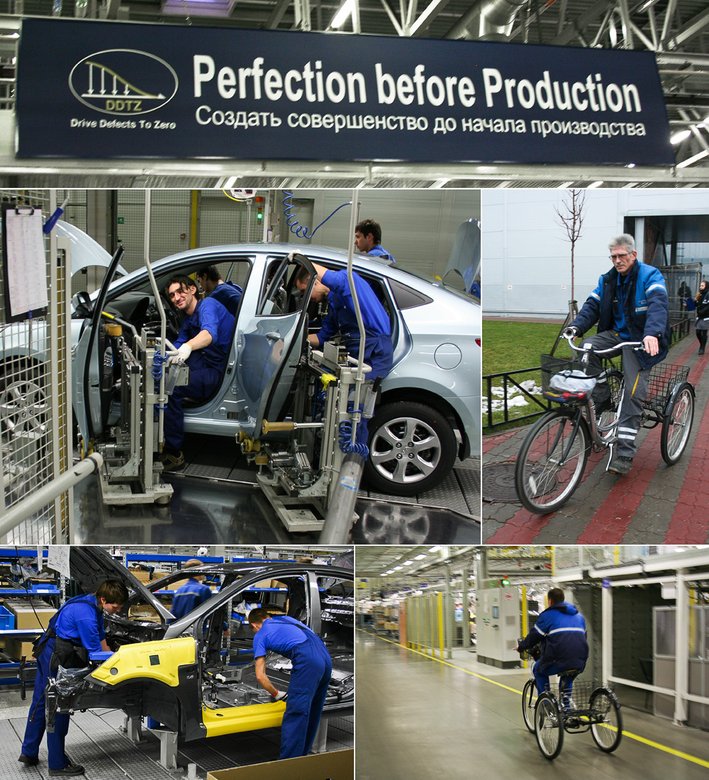
Что такое производство полного цикла? Обычно под этим подразумевают сварку и окраску кузовов, но в Hyundai считают, что настоящий «полный цикл» невозможен без штамповки, а потому на питерском заводе компании установлены четыре пресса, формующие 17 кузовных деталей для модели Solaris. Трудно поверить, но огромные машины обслуживают всего 34 человека! Чтобы получить нужную деталь, лист оцинкованной стали («черный» металл используется только для крыши) сначала попадает под самый мощный пресс усилием 2300 тонн, который вытягивает необходимую форму. Затем форму подправляют на двух других прессах, которые выдают усилие до 1000 тонн, а завершает процесс штамповки пробивка отверстий 800-тонной машиной.
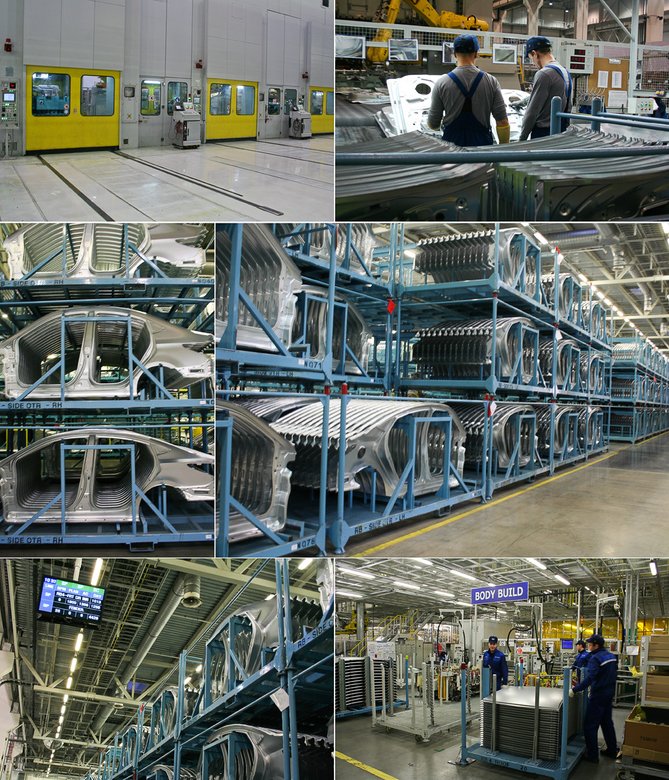
В цехе сварки присутствие человека также минимизировано — штампованные элементы «складываются» роботами Hyundai в кузова, а затем тщательно «провариваются». Однако настоящее царство мехатроники — это окрасочный комплекс: вот хитроумные устройства наносят герметик и мастику, вот кузов без помощи человека окунается в ванну с грунтом, вот змееподобные шланги наносят краску... Интересный момент: бамперы красят не только отдельно от кузова, но и вообще на другом предприятии (этим занимается производитель пластикового обвеса, компания Mobis). А если бампер окажется немного другого оттенка? «Это технически невозможно», — без сомнений отвечают заводчане и наглядно показывают, что колеры бампера и кузова совпадают стопроцентно.
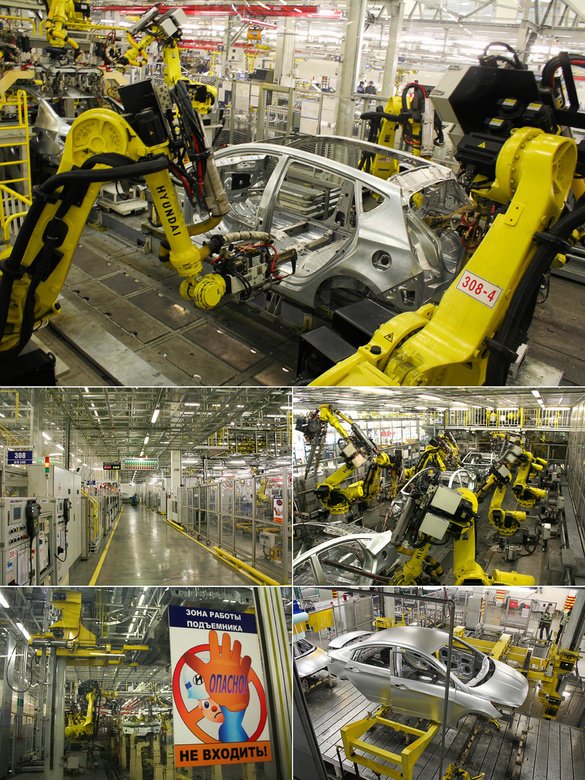
Окрашенный кузов сначала осматривают в световом тоннеле, тщательно выискивая возможные дефекты, а затем отправляют на сборочный конвейер. Так вот где работают живые люди! Впрочем, и здесь человеку помогают роботы: они наносят клеящий состав на стекла, помогают устанавливать переднюю панель и сиденья, «женят» кузов и подсобранную ходовую... Обнаружив дефект, любой (!) рабочий может остановить конвейер, но многие недочеты удается устранить на месте, а дефектные комплектующие отсеиваются заранее. Кстати, пройдясь по конвейеру, мы отметили, что российских комплектующих — примерно половина (в частности, отделка салона, сиденья, глушители, тормозные и топливные трубки), зато география остальных деталей и агрегатов крайне широка. Например, двигатели приходят из Китая, а колеса из Кореи. Наши наблюдения подтвердили и представители Hyundai: на сегодняшний момент уровень локализации превышает 45%.
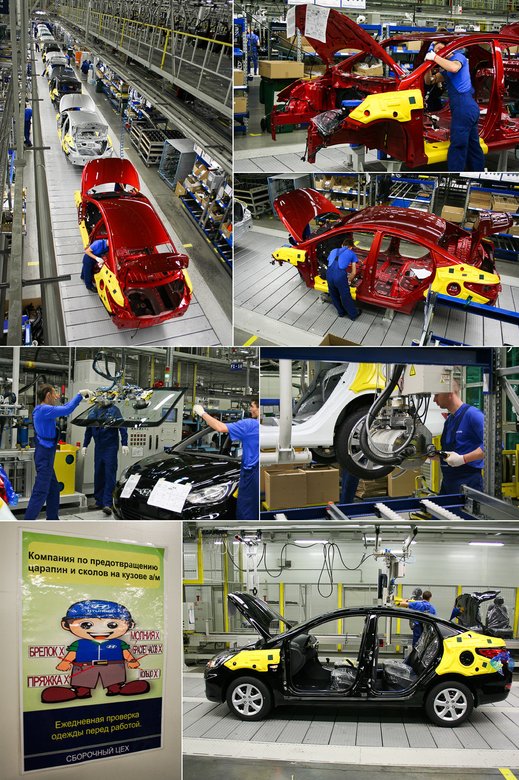
А вот и готовый «Солярис»! Но перед тем, как заехать на автовоз, каждая машина проходит обязательный тестовый пробег по заводскому полигону, затем она проверяется на герметичность в дождевальной камере и осматривается в световом тоннеле на предмет качества сборки и окраски. В итоге, от присвоения сваренному кузову VIN-номера до выхода готового Solaris проходят ровно сутки. А если считать от поступления стального листа на штамповку, то создание одного автомобиля занимает примерно 30 часов.
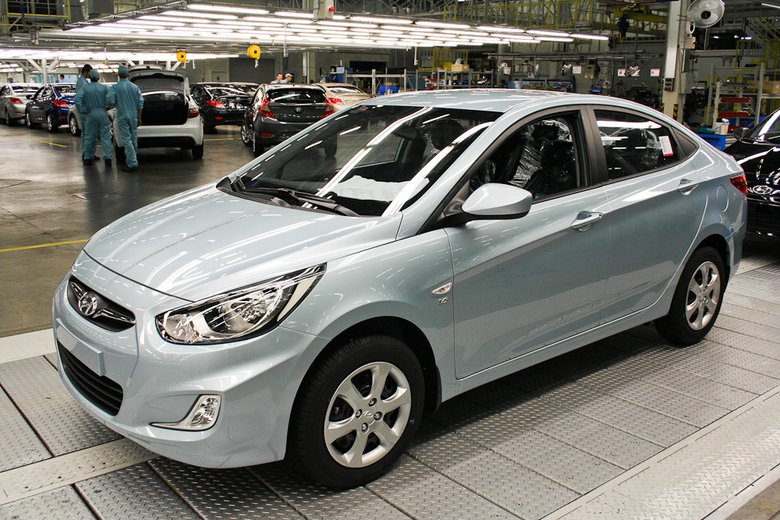
Но и россияне, и жители СНГ задаются одним вопросом: «Как правильно читать название Hyundai?» По словам представителей компании, изначально правильно говорить «Хёндэ», но, учитывая, что долгое время культивировалось произношение «Хёндай», корректными можно считать оба варианта.
Алексей Кованов, Оксана Эске
Фото авторов