Условия эксплуатации в России предъявляют повышенные требования к автомобилям. И дело не только в разных климатических зонах — машины у нас ездят и в суровых районах Крайнего Севера, где зимой нередки температуры ниже минус 50 градусов по Цельсию, и в засушливых местах, где летом стрелки термометров уходят за «40».
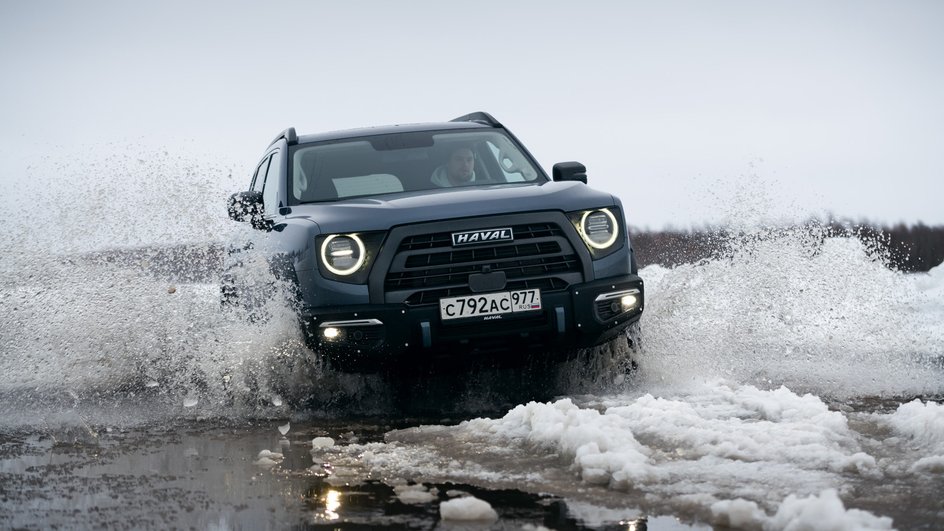
Дороги в отдаленных регионах тоже, в основном, имеют не асфальтовое, а грунтовое покрытие, что увеличивает нагрузку на кузов и агрегаты автомобилей. А самую большую угрозу для металлических деталей несет обработка противогололедными реагентами в зимнее время года — соляной туман буквально «съедает» их.
Поэтому адаптация автомобилей к российскому рынку требует серьезного и комплексного подхода: модернизацию систем охлаждения и отопления, добавление подогревов лобового стекла, задних сидений, руля и форсунок стеклоомывателя, доработку подвески и повышение антикоррозионной стойкости металлических деталей. Как это делают?
Человечество узнало о ржавчине еще несколько тысячелетий назад, когда появились первые железные орудия труда. Неприятный процесс образования коричневых и рыжих окислов на поверхности металла в результате его контакта с окружающей средой называется коррозией (от латинского corrosio, что означает «разъедание»).
На что влияет коррозия?
Постепенно стальные сплавы оказались основным конструкционным материалом, что сделало борьбу с коррозией одной из главных задач при эксплуатации мостов, зданий, трубопроводов, промышленного оборудования, судов и других транспортных средств, в частности, автомобилей. В случае с автомобилями коррозия снижает жесткость деталей, а это ухудшает не только управляемость машин, но и безопасность. Как с этим борются автопроизводители?
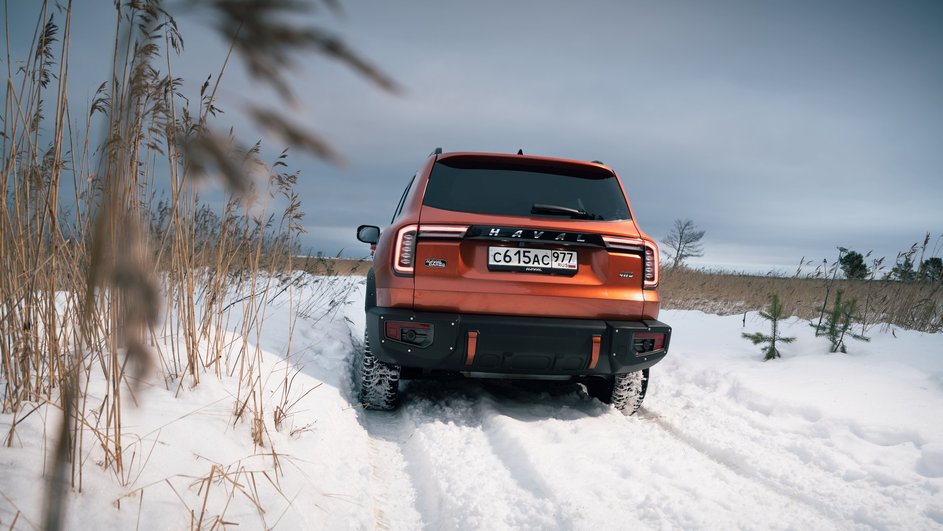
В борьбе с коррозией помогает цинк — покрытие из этого металла защищает стальные детали от контакта с кислородом и, как следствие, от образования ржавчины (окислов железа). Но появление оцинкованной стали не могло помочь автомобильной индустрии — детали из нее труднее сваривать и сложнее окрашивать, необходим специальный грунт.
Разумеется, никто не погружает кузов в расплавленный цинк — температура плавления этого металла составляет 420 градусов по Цельсию. Представляете, сколько энергии потребовалось бы, чтобы постоянно подогревать такую ванну, да еще и обеспечить работу оборудования и людей?
Купание железного коня
Выходом стало так называемое катафорезное грунтование — одно из самых эффективных решений, защищающих автомобильный кузов от коррозии. Разумеется, метод этот может быть реализован только на современном предприятии, потому что требует наличие специального оборудования.
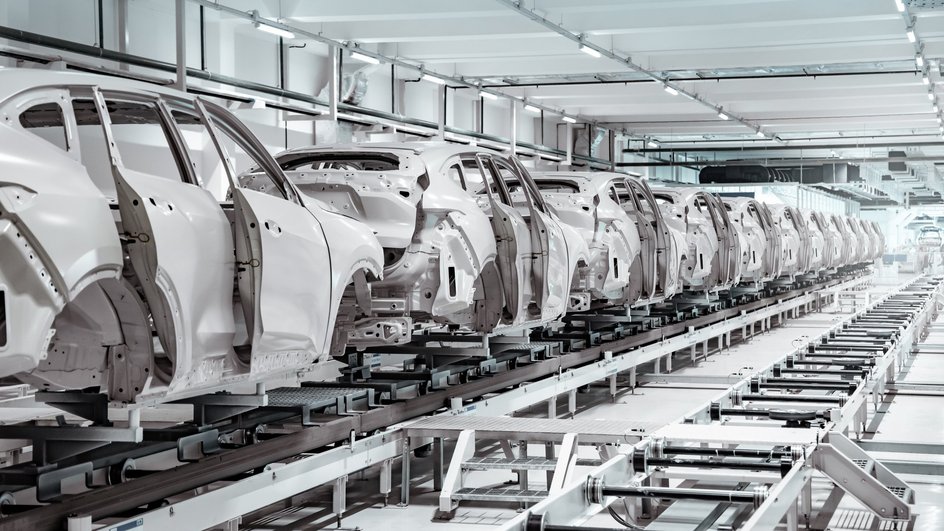
К примеру, ванна для катафорезного грунтования есть на производстве Haval. Для высокой коррозионной стойкости нужен и качественный металл, поэтому при производстве автомобилей Haval применяется оцинкованная сталь. Дальше штампуются детали, из которых в автоматизированном цехе роботами сваривается кузов. Затем он поступает в окрасочный цех, где и происходит «магия».
Готовый кузов очищается от окислов металла и инородных частиц после сварки, а также тщательно обезжиривается, проходя через специальный «душ» из химикатов, удаляющих попавшие на поверхность технические жидкости. Затем начинается подготовительный этап, состоящий из фосфатирования и активации, и, наконец, остов погружают в ванну, в которой в растворенном виде находятся частички грунта.
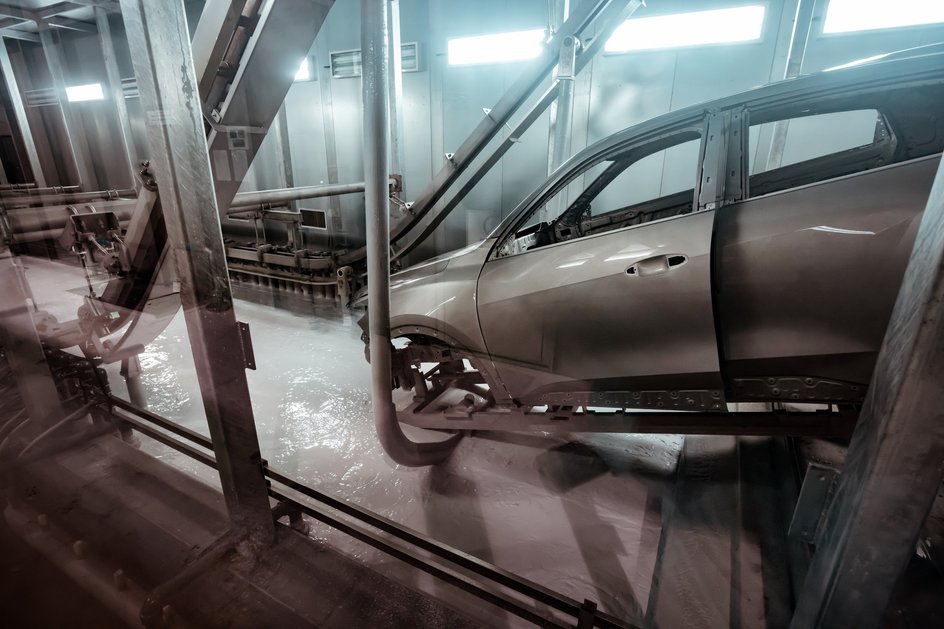
Процесс катафореза выглядит следующим образом: к кузову присоединяют анод (отрицательно заряженный электрод), а к самой ванне — катод с положительным зарядом, который и активирует грунт. Далее происходит электрохимическая реакция, в результате которой частицы грунтовочной смеси оседают на поверхности металла, покрывая его прочным защитным слоем.
Затем кузов ополаскивают, сушат и только потом он поступает в окрасочную камеру, где на него наносят эмаль и лак. Этот процесс также полностью автоматизирован, что позволяет в точности соблюдать технологию производства и исключить человеческий фактор.
Надежно ли такое покрытие?
На производстве Haval действует лаборатория физико-химических методов анализа, которая занимается испытаниями лакокрасочного покрытия. Окрашенные пластины подвергаются различным тестовым процедурам. Например, их выдерживают в климатической камере при температуре 47 градусов и влажности 96±2%. Кроме того, пластины помещают в «камеру солевого тумана» и оставляют до 1000 часов. Также проводят испытания на определение устойчивости лакокрасочного покрытия к воздействию бензина, антифриза, щелочи и кислоты. Лакокрасочное покрытие испытывают на сопротивление удару с помощью груза, эластичность и адгезию. Комплекс таких испытаний позволяет определить, насколько надежно лакокрасочное покрытие защищает металл.
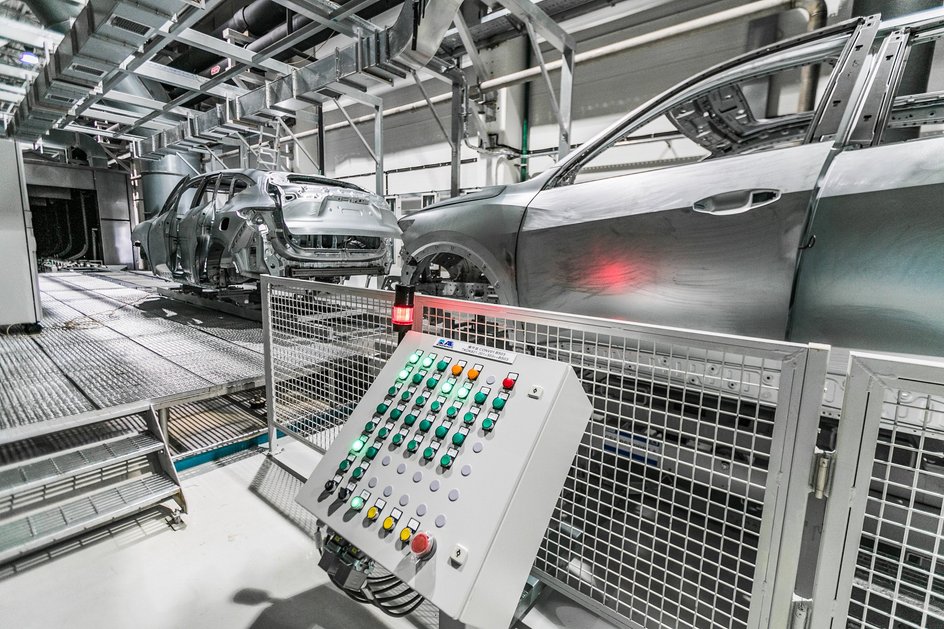
Качестве подтверждено испытаниями
Для того, чтобы подтвердить высокое качество антикоррозийной обработки, с сентября 2023 года по апрель 2024 года провели суровые проверки по методике, разработанной специалистами Центра испытаний НИЦИАМТ ФГУП «НАМИ»* на автополигоне в Дмитрове.
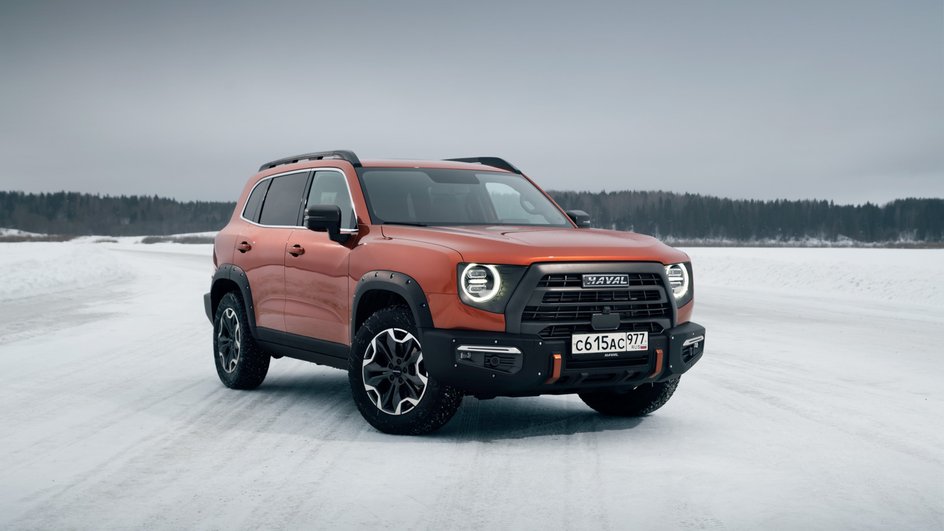
Участвовал в них серийный кроссовер Haval Dargo. Программа, рассчитанная на 127 ускоренных циклов коррозионных испытаний и соответствующая 12 годам реальной эксплуатации автомобиля, включала в себя проверки в камере соляного тумана и дорожные тесты на специализированных покрытиях — грунтовом, щебневом и каменистом.
В рамках испытаний Haval Dargo провел в коррозионной камере 762 часа, а общий пробег автомобиля составил более 14 800 километров. Перед началом теста на 12 контрольных точек кузова нанесли искусственные очаги коррозии — прорезы лакокрасочного покрытия до поверхности основного металла для наблюдения за развитием и динамикой проникновения ржавчины.
В начале каждого цикла Dargo помещался в коррозионную камеру в условия агрессивной среды типа «морской туман» при температуре 37±2°С, влажности 95±3% и воздействии 3,5−5% солевого тумана на 6 часов. Дополнительно перед началом движения и в конце пробега проводился двукратный проезд через мелководную ванну с солевым раствором.
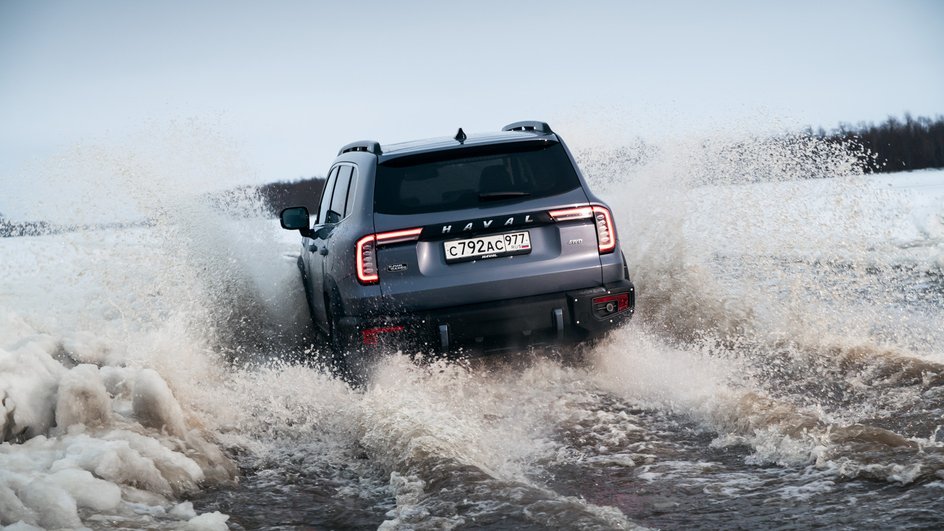
По окончании каждого условного «года эксплуатации» проводился контрольный заезд на тормозной стенд для проверки всех систем автомобиля. Кроме того, каждый раз измерялась глубина проникновения коррозии в зонах искусственных очагов.
По итогам испытаний был проведен глубокий анализ коррозионной стойкости элементов автомобиля. Контрольный осмотр включал в себя замеры глубины проникновения ржавчины и распространение подпленочной коррозии. Также был осуществлен разбор автомобиля до окрашенного кузова для оценки его общего состояния, а затем — и самого кузова для анализа состояния внутренних поверхностей деталей и его скрытых полостей.
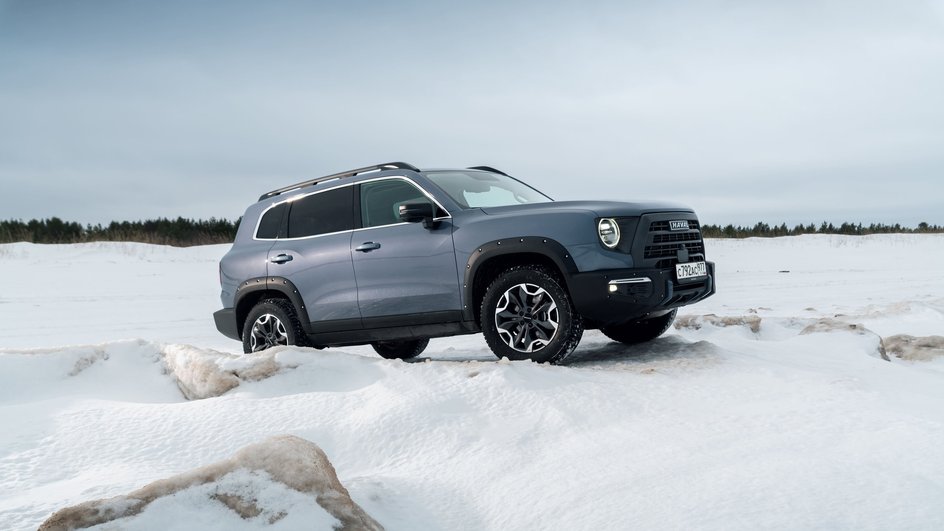
По результатам испытаний специалисты внимательно изучили Haval Dargo и пришли к выводу, что кузов автомобиля качественно подготовлен и окрашен, благодаря чему обладает высокой коррозионной стойкостью. Поэтому Haval дает гарантию 6 лет от сквозной коррозии, причем независимо от пробега.
* Центр испытаний НИЦИАМТ ФГУП «НАМИ» — это 15 типов и разновидностей испытательных дорог общей протяженностью более 110 км на площади 25 кв. км. Единственный в России и крупнейший в Европе испытательный центр, моделирующий практически все многообразие специфических дорожных условий эксплуатации автомототехники России.
Реклама ООО «Хавейл Мотор Рус» ИНН: 7729763331 erid: 2VtzqwtNksk.